February 2025 - MABA Biosolids Spotlight
Provided to MABA members by Bill Toffey, Effluential Synergies, LLC
SPOTLIGHT on the UAJA Biosolids Project
For now, at least, it is simply called the “Biosolids Project.” But by any standard, the comprehensive set of treatment innovations underway in State College, Pennsylvania, deserves superlatives. This “project includes advanced digester, dryers, food waste receiving, and biogas recycling, meeting every definition of The Utility of the Future Today or that of a Circular Water Economy facility, definitions that catch global attention among water leaders and that call to mind large, well-known projects in Los Angeles, Milwaukee, and Raleigh. The project includes descriptors that feature “energy,” as in facilities described in previous MABA SPOTLIGHTS, such as the WSSC Water’s Piscataway Bioenergy Facility, Rahway Valley Sewerage Authority’s food waste augmentation project and DC Water’s Bloom product and Bailey Bioenergy Facility. But these are facilities with large service areas, not the modest base of 14,000 connections of UAJA. Indeed, UAJA can expect its “biosolids project” will catch wide attention for being so clearly a template for hundreds of comparatively small public agencies across the country.
The University Area Joint Authority (UAJA) provides wastewater treatment and biosolids management services for State College, Pennsylvania, and much of the surrounding Centre County region. Under the leadership of executive director Cory Miller and a supportive, engaged board of 10 trustees, the UAJA has embraced sustainability, has a forward-thinking approach to watershed management and takes a leadership role in biosolids management.
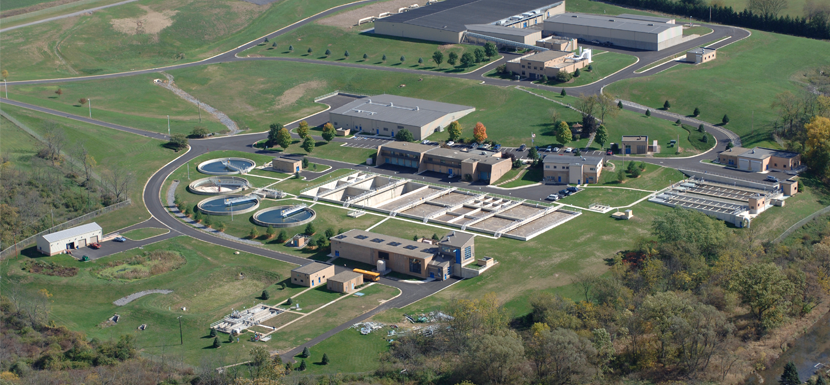
Aerial view of UAJA showing, in the upper part of the frame the composting building which was removed in 2024 for construction of the “biosolids project.”
Recognizing that UAJA’s composting infrastructure was nearing its useful life, yet remaining committed to making an exceptional quality product for soils in the community and the region, UAJA undertook a comprehensive planning study for biosolids treatment options. Miller and his board looked to an expanded role for UAJA as a regional organic processing facility, building on the base of a daily flow averaging 5.3 million gallons and an annual biosolids production of 2,400 dry metric tons. Considering as an option taking in wastewater solids and organic wastes from a wider region, the UAJA saw that it could better fulfill its role supporting economic and community development as well as good environmental quality.
Results of this decade-long visioning and planning has been “solid,” with UAJA embarking on a showcase bioenergy facility. The progress on this project was recently reported by the local newspaper, the Centre Daily Times: “An $81M project underway at UAJA will turn waste into renewable energy. Here’s how.”
Miller frames the case for the UAJA transformation in this way: “Eighty-one million dollars may be a scary number, but the Authority concluded the new plan is the best alternative for the community. It is affordable, based on revenue bonds supported by the rate payers of the system. In Pennsylvania, being on the leading edge means doing things without grant money. The compost facility was a game changer in its day but after nearly 30 years, it was all spent.”
The UAJA bioenergy vision has multiple features. The vision for solids is high-rate digesters for wastewater solids and food waste, biogas collection and treatment to pipeline quality, biosolids dryers with capacity to serve as a regional facility, and an excellent soil product that satisfies the demand of long-standing compost customers. No small part of the program is revenue from accepting food waste and digested solids from nearby agencies, but also added to the pro forma is sale of digester gas supplied to the nearby gas pipeline, biogas which commands a high price when cleaned to natural gas standards.
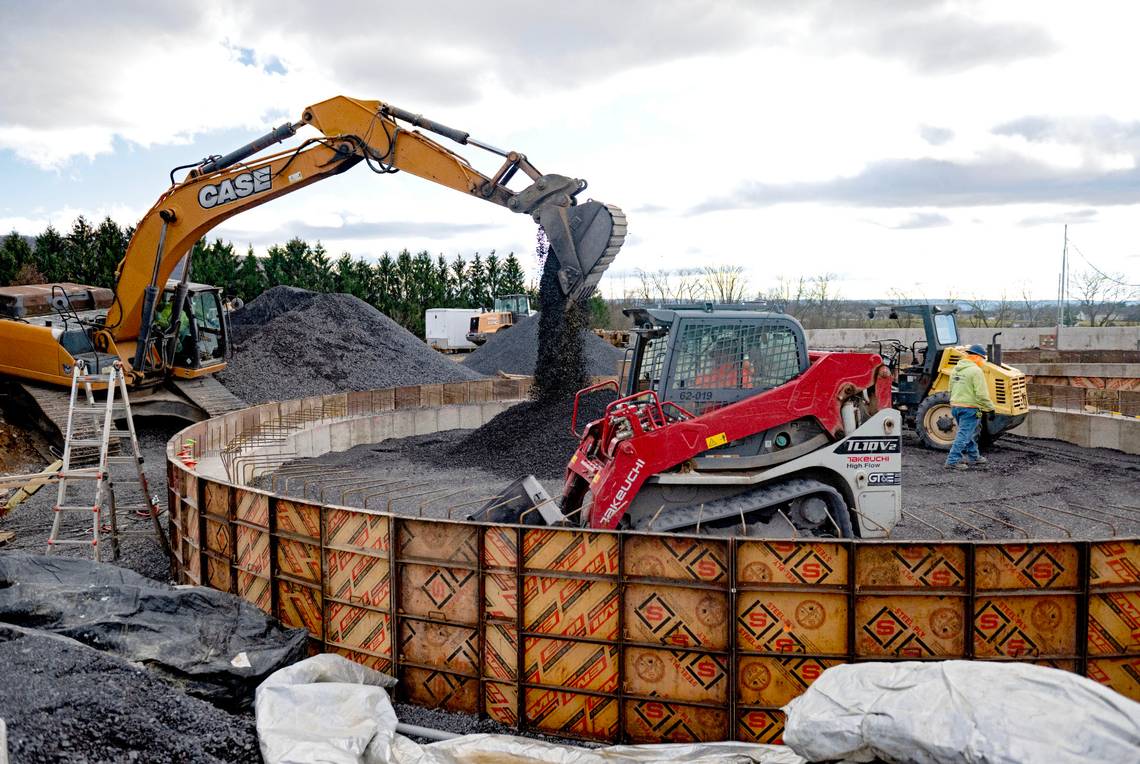
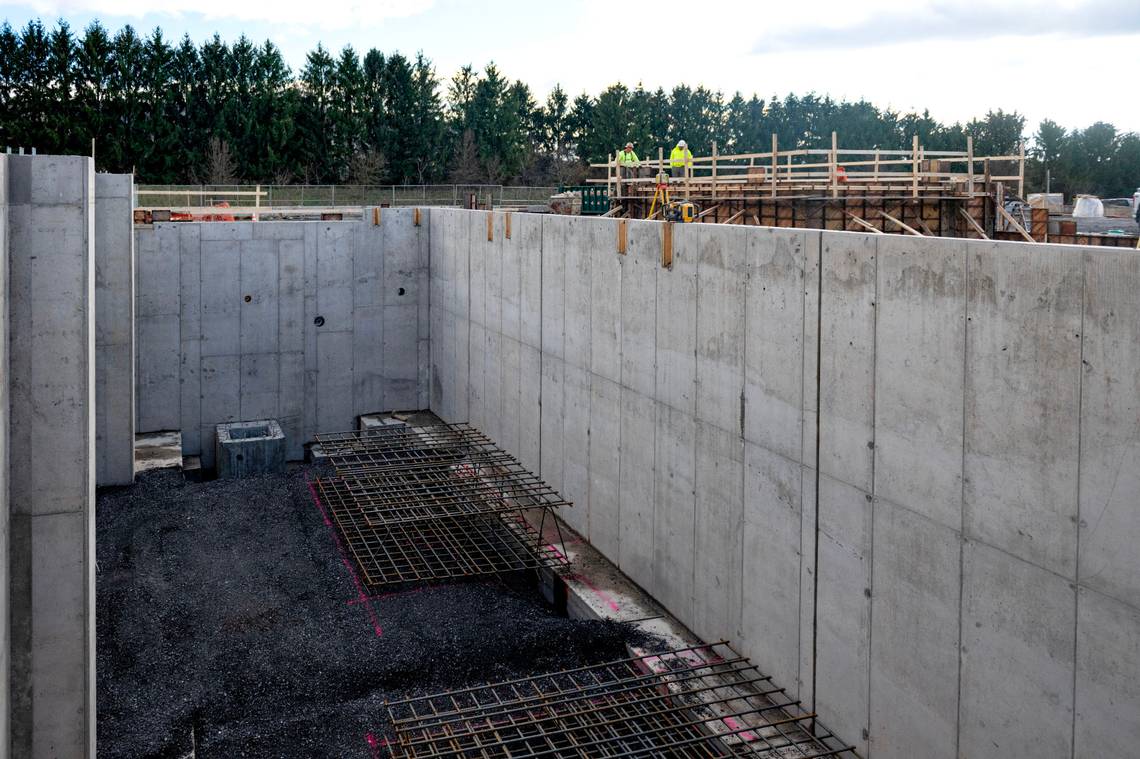
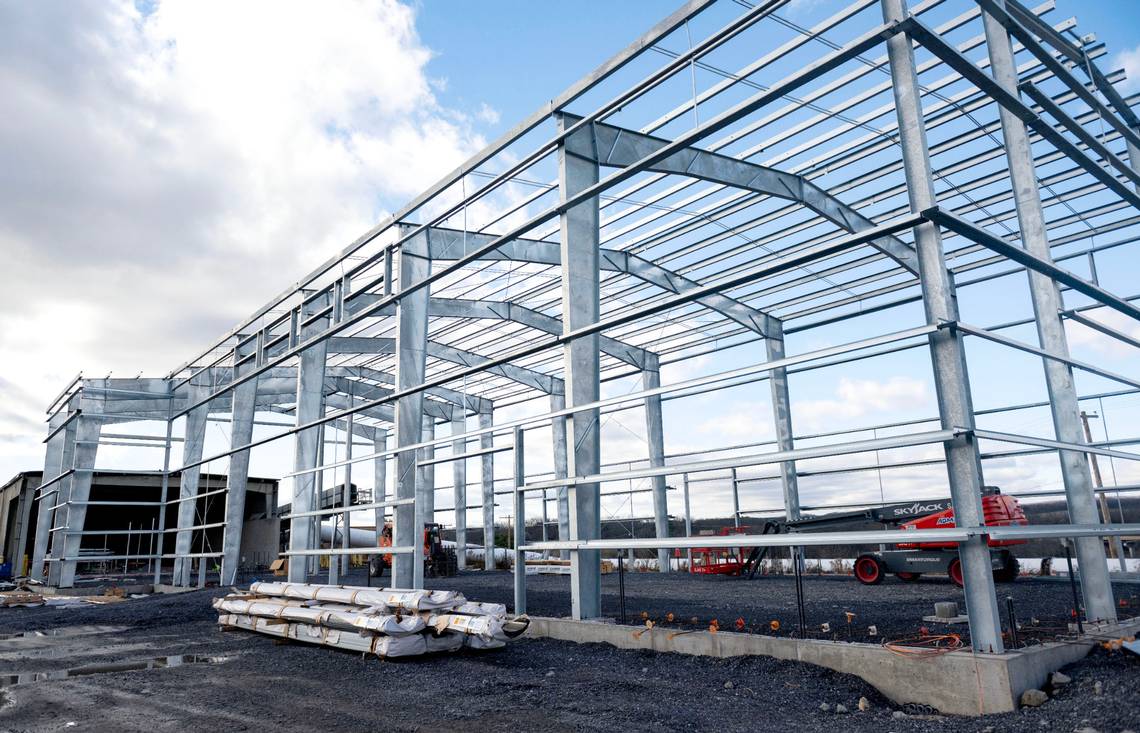
This set of photographs is from a Centre Daily Times article of “An $81M project underway at UAJA will turn waste into renewable energy. Here’s how” (12/12/2024), with pictures showing construction underway on anaerobic digesters (a), food waste receiving (b), and the drying building (c)
Revenue from tipping fees for food waste will in part pay the way for the capital costs in the receiving and processing facilities. The tipping fee set by UAJA for food waste disposal is set by the marketplace, as it is an incidental operation to wastewater treatment, which otherwise has a publicly set uniform rate for wastewater disposal This gives UAJA flexibility in its revenue for this operation, with daily adjustments to optimize digestion feed, to achieve microbial stability and to keep digesters at peak performance, while avoiding negatives, such as foaming.
UAJA will work closely with the Centre County Recycling and Refuse Authority. UAJA’s facility is prepared to partner with CCRRA to reach its goal to divert organic waste collected from households in the county from landfills. UAJA anticipates developing a steady source of pre-consumer commercial sources, as from supermarkets and manufacturers.
With the installation of the belt drying processes, UAJA will be providing regional biosolids services. Once in operation, UAJA will be accepting digested dewatered sludges from nearby boroughs of Tyrone and Bellefonte, along with the Moshannon Valley Joint Sewer Authority in Phillipsburg. UAJA will dry the biosolids and market the product as a Class A EQ soil product, mostly as a turf grass management product. Compared to compost, which has been very popular over more than two decades, UAJA expects its dried product to be in good demand also, with less volume to manage than compost. As was the case with compost distribution, commercial users will arrange their own transportation. UAJA expects its biosolids product to go out the door with little focused marketing on the part of UAJA. Miller has already received a request from one user to purchase the entire supply.
Miller believes the UAJA will be a role model for other communities. UAJA is a medium sized utility, with a flow rate typical of many boroughs and towns in the mid-Atlantic region. As UAJA creates a role for itself as an organic waste processing center, it is an example of goal fulfillment for recycling often sought by local leaders, namely the reduction of organic waste disposal in landfills. Miller advocates for public agencies engaging in master planning for biosolids: “Master planning really doesn't cost that much, and it opens doors for long term solutions.”
Innovative technologies motivate the UAJA staff. Miller is committed to bringing on people who are challenged by new technology and who value continuous learning. The world-class bioenergy facility is that kind of attractor for talented operators. UAJA’s take on “first in class” technologies is that companies with such technologies have a stake in ensuring smooth operations and in helping ensure authority staff are well-trained.
UAJA invites the community for tours of its facilities. It has well over 1000 visitors annually, including university students. Miller is particularly committed to tours for fifth grade students who are studying water. UAJA is a regular field trip destination, showing the young students not only the impressive array of tanks and pumps, but the control rooms, the laboratories and machine shops as well. He has witnessed firsthand the value of children and their parent chaperones learning of the wastewater treatment enterprise, as they are or will be future ratepayers who appreciate the value of wastewater services. He recalls early in his career one 5th grader who grew up to become an elected township supervisor in his service area.
About the role of UAJA in the State College community, Miller explains: “The game is not just sewage, but also life quality, business development, and environmental sustainability. The mindset across the wastewater industry ought to be that we recognize what we are really doing is improving the quality of life and local economy along with enhancing the environment.”
The UAJA project has as its role model the amazing Hermitage Food Waste to Energy Facility and Wastewater Plant in Hermitage, Pennsylvania, a MABA member agency. Tom Darby, executive director of this small agency with a big game plan, has pioneered the role that Cory Miller is undertaking. Hermitage Borough has transformed a conventional wastewater plant into a regional processor of commercial food waste, and in so doing has become a reference facility for key equipment -- food depackagers, high solids digesters and biogas collection and clean up systems. The Hermitage facility is well described in its own brochure, and engaging YouTube video, and professional case studies (Food Waste Co-Digestion at Hermitage Municipal Authority (PA) Business Case Analysis Snapshot).
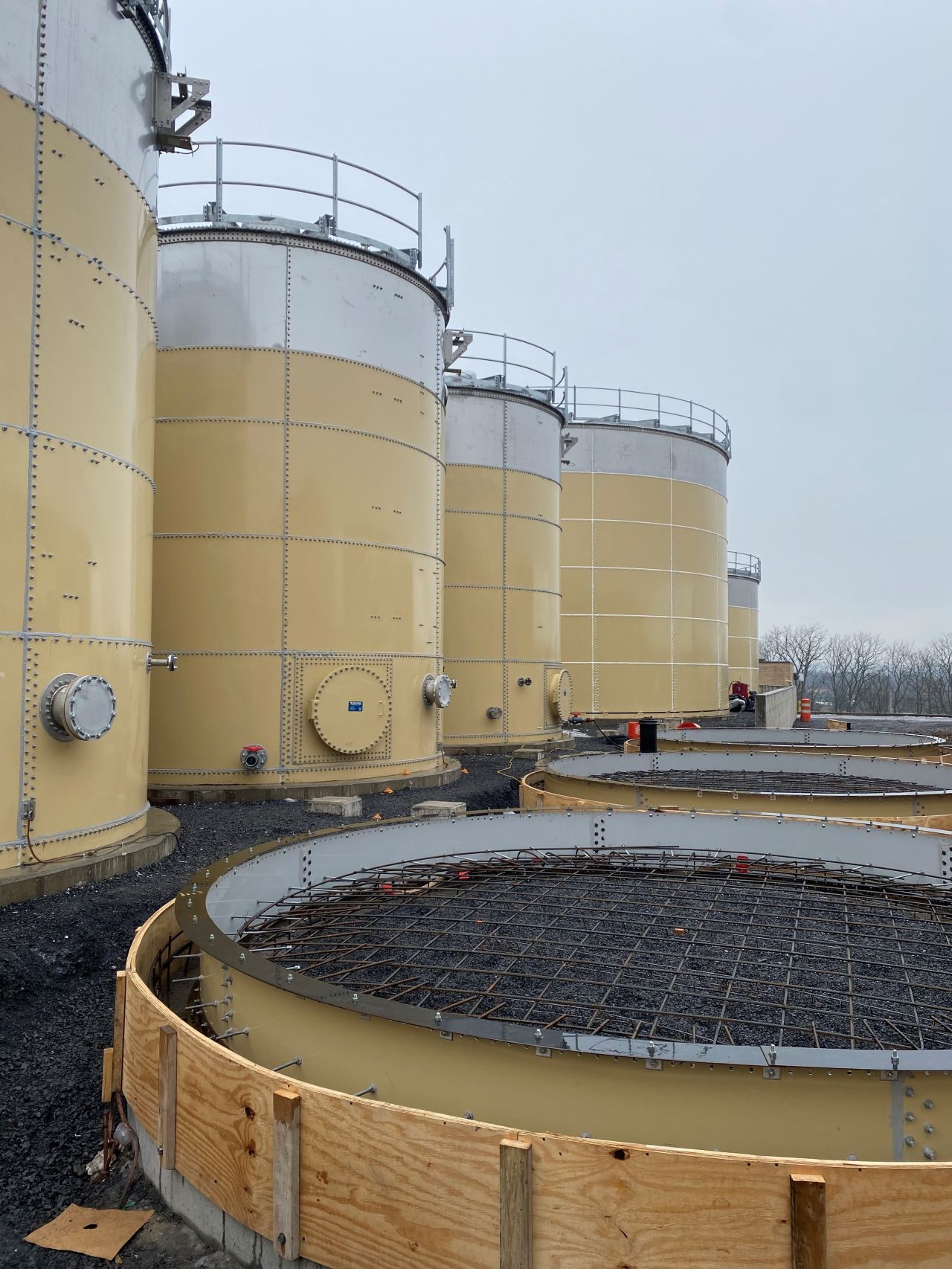
Biological hydrolysis is a key aspect of the Veolia two-step anaerobic digestion system under construction at UAJA, that can accommodate the high strength organic feedstocks from food waste and wastewater solids
While Darby was the force behind this facility, he was aided by engineering wizard Jason Wert, senior engineer with RETTEW, of State College, Pennsylvania. RETTEW, a MABA member, has had deep “hands on” experience with “waste to energy” at Hermitage that Wert has been able to apply to UAJA. Wert has emphasized several key features in the design of the UAJA waste-to-energy system, informed by the Hermitage experience. Anaerobic digestion, provided by Veolia, includes their Monsal biological hydrolysis process. This process allows for two stage digestion of the incoming wastewater solids, separating the hydrolysis and acid formation steps from methanogenesis, optimizing in the first stage for microbial destruction of complex organic matter before feeding digesters in the subsequent gas production stage. In so doing, UAJA can separately process wastewater solids and slurried food waste in separate digesters. This feature thereby enables operators to distinguish biogas derived from food waste from biogas derived from wastewater solids, a distinction that has revenue implications down the line. This separation also allows for processing times and temperatures to reflect the inherently different digestibility of the two feedstocks.
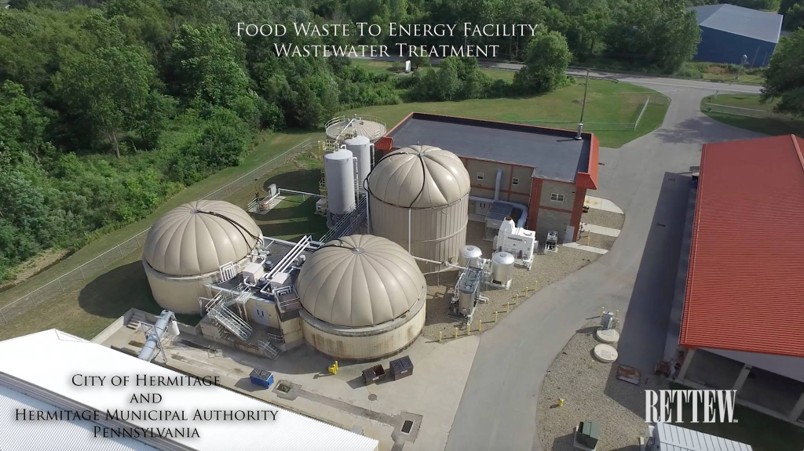
This is an aerial photograph of the Hermitage Food Waste to Energy facility at the borough wastewater plant which is a model for the project underway in State College.
One elaborate feature of the UAJA facility, compared to most municipal co-digestion operations, is the scale of the food waste processing capabilities. Harnessing Darby’s experience at Hermitage, UAJA will be using the Veolia Excrusor Food Depackaging System, an industrial scale system more commonly deployed at commercial solid waste facilities than wastewater plants. This equipment will allow UAJA, as with Hermitage, to accept packaged food products that require disposal, separating metal, plastic, and paper packaging from food waste, and thereby decontaminating slurried feed stock ahead of the digesters. The food waste processing area, with its enclosed food waste acceptance area, the Ecrusor and the slurry tank, is separate from the acceptance area for municipal biosolids cake. Cake will be received by UAJA from other wastewater plants for drying in Veolia BioCon, a belt dryer system that is another element of the new solids system producing a Class A EQ product for marketing. While the current plan of operation does not include digested food waste drying, this is a possible future step.
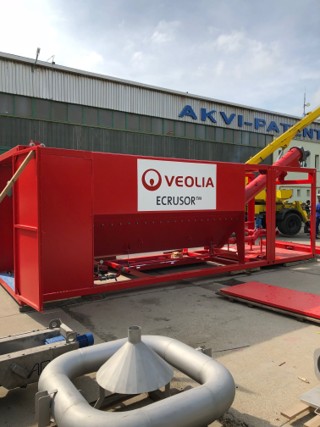
A key to the food waste receiving facility at UAJA will be the Veolia Excrusor that “depackages” commercial food waste, effectively separating organic materials from metals and plastics that are in packaging, and in use at Hermitage.
Biogas from digesters has maximum revenue potential when brought to “pipeline standards.” This is an elaborate set up for removing moisture and CO2, and for removing gaseous contaminants, notably hydrogen sulfide and siloxane, such that the biogas is transformed into Renewable Natural Gas, essentially indistinguishable chemically from its fossil-sourced gas.
Veolia is clearly a key part of the UAJA development as UAJA is installing Veolia’s first Biological Hydrolysis system at a wastewater facility in North America . This arises from the good track record of high solids two phase digestion at Hermitage and the success of Ecrusor equipment. But the selection of an integrated system from Veolia is in part due to the development of commercial scale biogas production facilities using Veolia equipment in the mid-Atlantic region. Veolia’s Nick Bonkoski, a MABA Board member, has for many years been an advocate and technical salesperson for the Monsal Biological Hydrolysis methods of digestion, having learned the trade from his father William Bonkoski, who spent almost 50 years in the business. Bonkoski has seen the food waste-to-biogas industry take off over recent years. He points to two privately developed projects in the region that are under construction: Linden (New Jersey) Renewable Energy Project, the brainchild of RNG Energy Solutions, and the American Organic Energy digester project in Yaphank, New York, a project headed by Charles Vigliotti, who has provided leadership in the composting arena for decades with the Long Island Compost facility. These facilities draw upon the vast volumes of food waste generated in the New York / New Jersey metropolitan region. But even boroughs the size of State College produce a volume of organic wastes suitable as a feedstock for anaerobic digestion.
UAJA is in the mid-point of its solids system transformation. In Spring 2023, the last of UAJA biosolids was put through the enclosed compost system, and landscape customers worked through the final compost inventory by Summer 2024. A year ago, in January 2024, contracts were signed, and by mid-year, the compost building had been removed, and foundational work began for the dryers and waste handling areas began. Later in 2024, construction of hydrolysis and digester units began. Much of the construction is expected to be completed by the end of 2025, with start up extending into mid-2026.
One year from now we ought to be receiving our invitations to the opening of this state of the art digestion facility. It will surely become the destination of choice for biosolids managers throughout the Mid Atlantic. Perhaps UAJA will have a naming contest for this facility. The ”biosolids project” could become the “Centre Region Ecofactory for Food Waste and Wastewater Solids Transformation to Bioenergy and Biofertilizer.” We have a year to work on this name…
For more information, contact Mary Baker at [email protected] or 845-901-7905. |